When Beck Crespel set out to overhaul its Armentières workshop, the goal wasn’t just to reorganise - it was to modernise operations, boost efficiency and reduce environmental impact. In line with CTB Group’s ongoing ESG commitments and drive for continuous improvement, the team spent nine months redesigning workflows to reduce waste and energy consumption and improve teamwork.
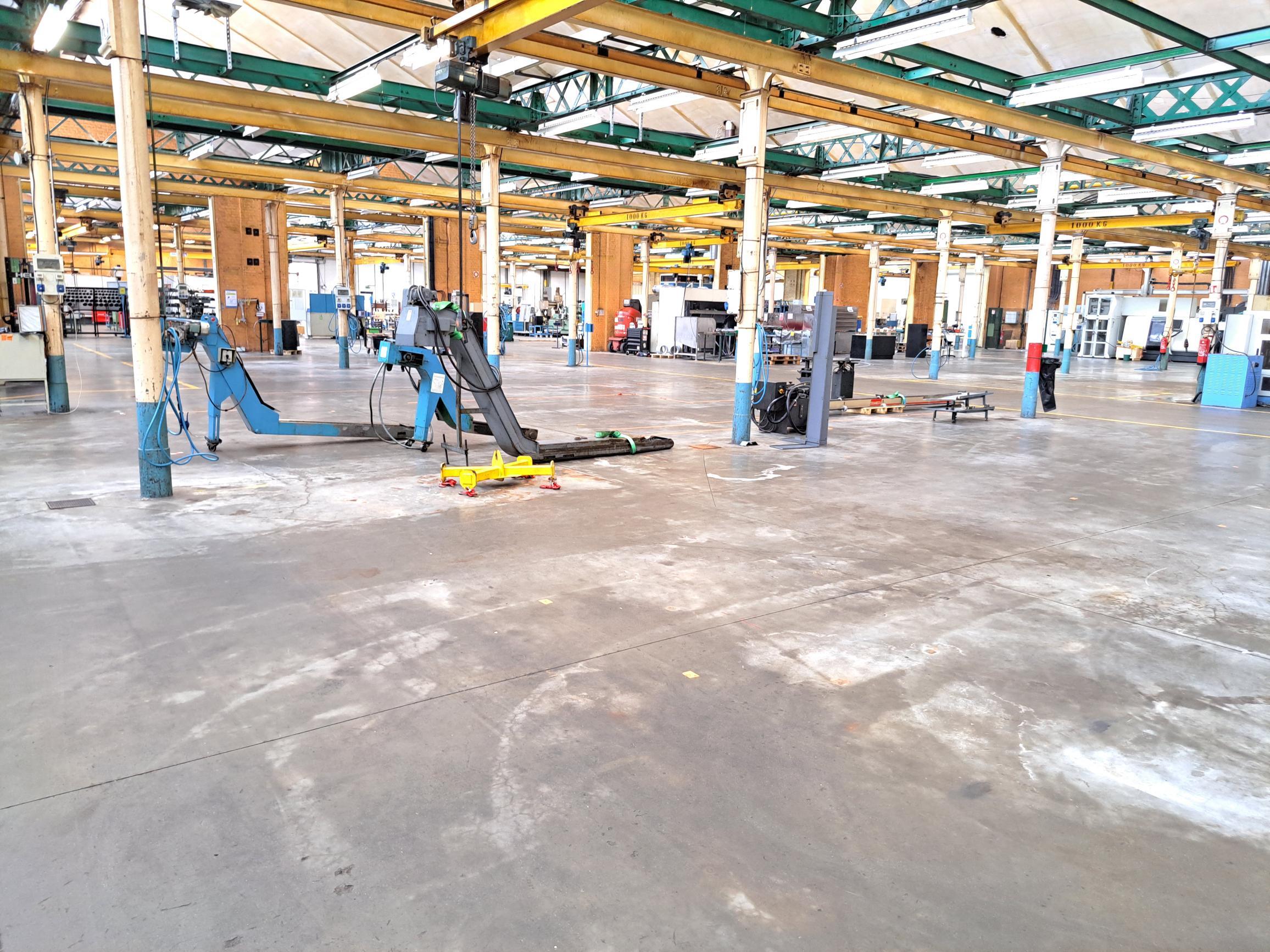
Operational Efficiency
Beck Crespel’s transformation began in 2021 with the installation of eight new MAZAK CNC machines - part of a €1.2 million investment in upgrading the plant’s production capabilities. By offsetting part of the cost through the sale of older equipment, the team kept the upgrade financially and environmentally sustainable.
In 2024, the focus shifted to optimising the factory layout. At the time, key operations like quality control and barfeeders were split across separate buildings - a setup that slowed workflows and complicated logistics. The reorganisation brought all machinery into a single, unified space. In total, 55 machines were moved to streamline production and improve team coordination on the shop floor.
These changes have sharpened production, cut down on errors, brought costs down, and helped teams stay better connected on the shop floor.
Team Culture and Collaboration
Bringing key operations under one roof hasn’t just improved workflows - it’s also changed how teams work together. With line managers now closer to the shop floor, support is quicker and decision-making is more visible. Teams are positioned side by side, which has encouraged faster communication, stronger collaboration, and a greater sense of shared responsibility.
As a result, problems are spotted and dealt with sooner, and teams stay more in tune with what’s happening around them, creating a more connected, responsive working environment.
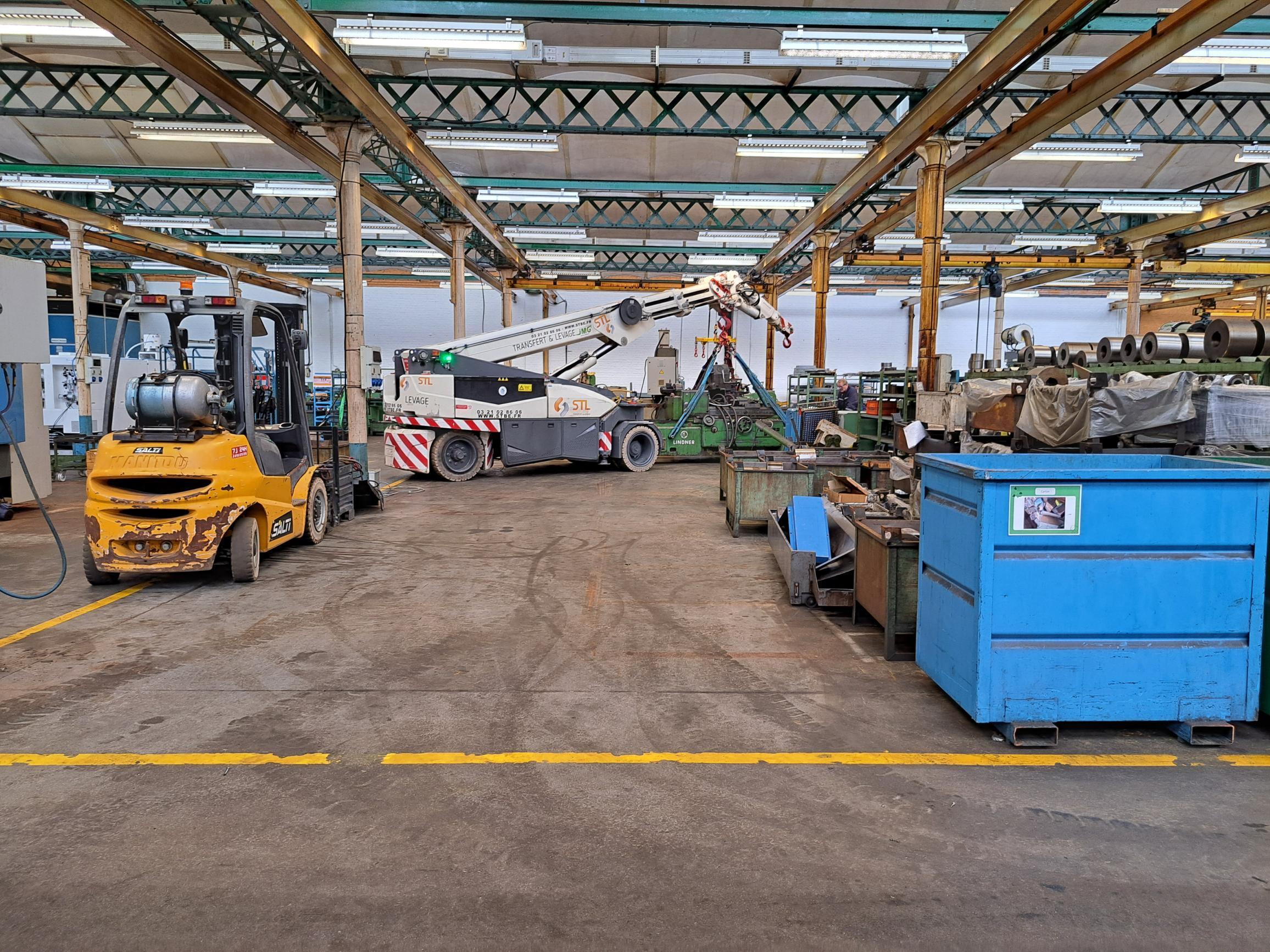
Sustainability and Product Quality
The redesign also supports CTB Group’s wider ESG and sustainability goals. By consolidating operations into a single building, the site now uses less energy for heating and lighting - and with newer, more efficient machinery, overall energy demand has dropped while productivity has improved.
Integrating quality control directly into the workshop has also raised the bar for product quality, helping to identify issues earlier and ensure more consistent, reliable output.
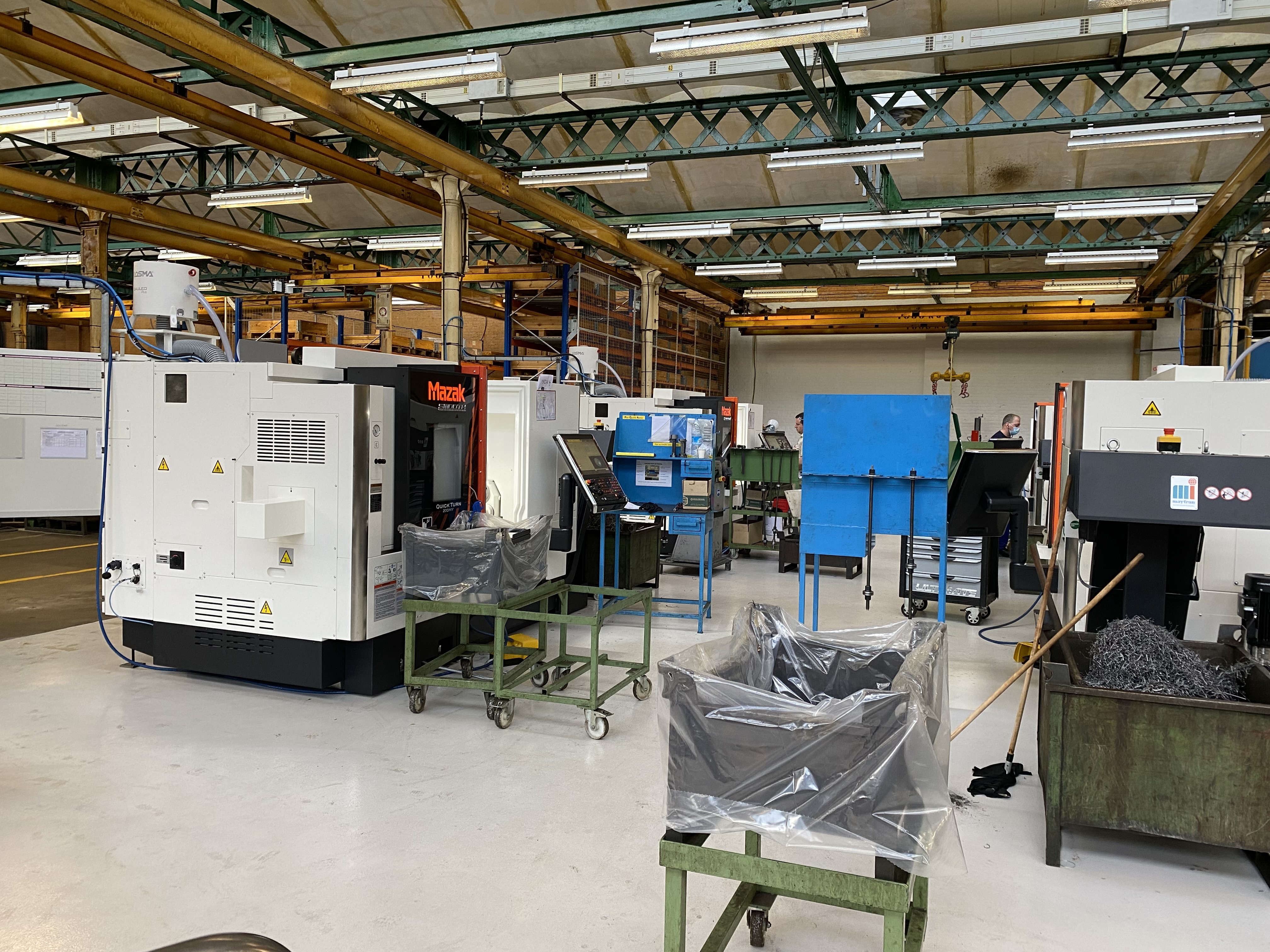
Next Steps
The nine-month transformation of the Armentières workshop has delivered measurable improvements across efficiency, collaboration, sustainability, and quality control. The next phase will focus on visual management - introducing clear walkways, defined safety zones, and visual cues to track the flow of materials and activity across the site. These changes will make it easier for teams to stay aligned in a busy environment and support quicker, more informed decisions on the factory floor.
This upgrade is part of a broader shift in how CTB Group operates, communicates, and delivers on its sustainability goals. Want to understand the bigger picture behind changes like this? Read our latest ESG report to see how operational improvements at sites like Armentières align with our long-term commitments to sustainability, quality, and people.